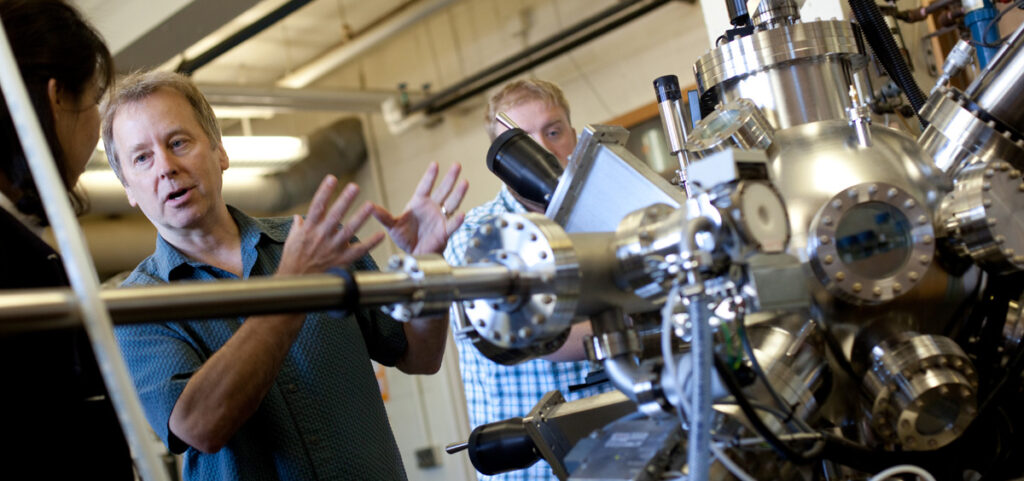
Popular Mechanics’ prediction took considerably more than 10 years to come true, but today’s flat-panel screens have gone well beyond that early vision. Some of them are nearly as big as a living room wall. They bring us unimaginably sharp detail, from the spots on butterfly wings to the grimace on a linebacker’s face.
This technology — whether hooked up to your cable feed, DVD player, wi-fi or computer — is also becoming integral to daily life. It increasingly provides the platforms on which we shop, share photos, read books, keep up with friends, play games, manage finances and work. In 2011, the global flat-panel screen industry shipped more than $120 billion worth of products, enough to cover nearly 16,000 football fields.
However, our love of flashy high-res has a dark side. Manufacturing the semiconductors behind these electronic systems produces waste, lots of it. “The electronics and solar industries build devices where the materials input is very high relative to what ends up in the product. There’s tremendous amounts of waste and very high energy input,” says Doug Keszler, Oregon State University chemist.
Keszler and a team of scientists and engineers at Oregon State and the University of Oregon are leading a national consortium bent on greening the flat-panel display industry. In their future, windows, mirrors, walls and counters could display messages and harvest solar energy. “We’re trying to turn this industry into a truly zero-waste proposition while improving performance,” says Keszler, a principal scientist in the Center for Sustainable Materials Chemistry (CSMC). “We’d like to do electronics the size of a wall. The question is: How do you do that efficiently without producing even more waste?”
Startups Provide Jobs
The CSMC has already produced significant results: a metal-insulator-metal diode (a kind of electronic switch) that outperforms the fastest silicon-based semiconductors; water-based manufacturing techniques that reduce waste and improve productivity; high-resolution fabrication processes that forge thinner electronic components. With research roots going back more than a decade at OSU and UO, the center has spun off two startup companies, generated more than a dozen U.S. patents and developed an educational partnership to inspire more Oregon high school students to attend college. It also helps graduates to create their own careers. In cooperation with the National Collegiate Inventors and Innovators Alliance, CSMC students join business leaders in the chemical and electronics industries to identify commercial opportunities stemming from research.
“About two-thirds of all Ph.D. graduates in the physical sciences now find their first job in a startup company,” says Keszler. “There is very little education to prepare students for that career path. We train them to recognize market value in their research, so they can work effectively with entrepreneurs and business development people.”
Two startups have already hired the center’s graduates. Amorphyx (www.amorphyx.com) is commercializing a new electronics manufacturing process that limits the production of unwanted industrial byproducts. Moreover, it trims a six-part process to two steps, offering the possibility of tripling production capacity in an existing facility.
In collaboration with another spinoff, Inpria (www.inpria.com), the center has broken a barrier in high-resolution circuitry, going below the 20-nanometer scale and enabling computer chips to accommodate more functions at higher speeds.
These achievements reflect gains reported by Oregon State engineer John Wager, physicist Janet Tate, graduate student Randy Hoffman and other researchers as early as 2003. They noted that transparent thin-film transistors made of zinc oxide could lead to new kinds of liquid-crystal displays, the dominant type of flat-panel screen. In 2006, HP licensed the technology and has been developing applications in collaboration with OSU.
At UO in 2003, researchers in Darren Johnson’s chemistry lab discovered a solution-based process for making nanoclusters, leading to the possibility that new semiconductors could be made without hazardous chemicals. Jason Gatlin, the UO graduate student who discovered the process, instigated a new UO-OSU collaboration when he shared his findings at a conference sponsored by the Oregon Nanoscience and Microtechnologies Institute.
“We’re pushing the boundaries of science and seeing things no one has ever seen before,” says Keszler. “There’s a lot of joy in the intellectual exchanges in such a diverse group.”
To attract more young scientists to their journey, CSMC students will begin working with Hermiston High School teacher Lisa Frye and her chemistry classes this fall. They will provide support, advanced instruction and resources to inspire high-school students to consider careers in science.
“What we’re after over the next 10 years,” says Keszler, “is to put the (industrial) ecosystem together that allows you to print electronics on flexible glass. They will be high performance, durable, and include applications such as solar collectors.”
We’ve come a long way from the futuristic idea of hanging TV screens like paintings on the walls of our homes.