This week we have a PhD candidate from the materials science program, Jaskaran Saini, joining us to discuss his work on the development of novel metallic glasses. But first, what exactly is a metallic glass, you may ask? Metallic glasses are metals or alloys with an amorphous structure. They lack crystal lattices and crystal defects commonly found in standard crystalline metals. To form a metallic glass requires extremely high cooling rates. Well, how high? – a thousand to a million Kelvin per second! That high.
The idea here is that the speed of cooling impacts the atomic structure – and this idea is not new or limited to just metals! For example, the rocks granite, basalt, pumice, and obsidian all have a similar composition, but different cooling times. This even gives Obsidian an amorphous structure, which means we could probably just start referring to it as rocky glass. But the uses of metallic glass extend far beyond those of rocks.
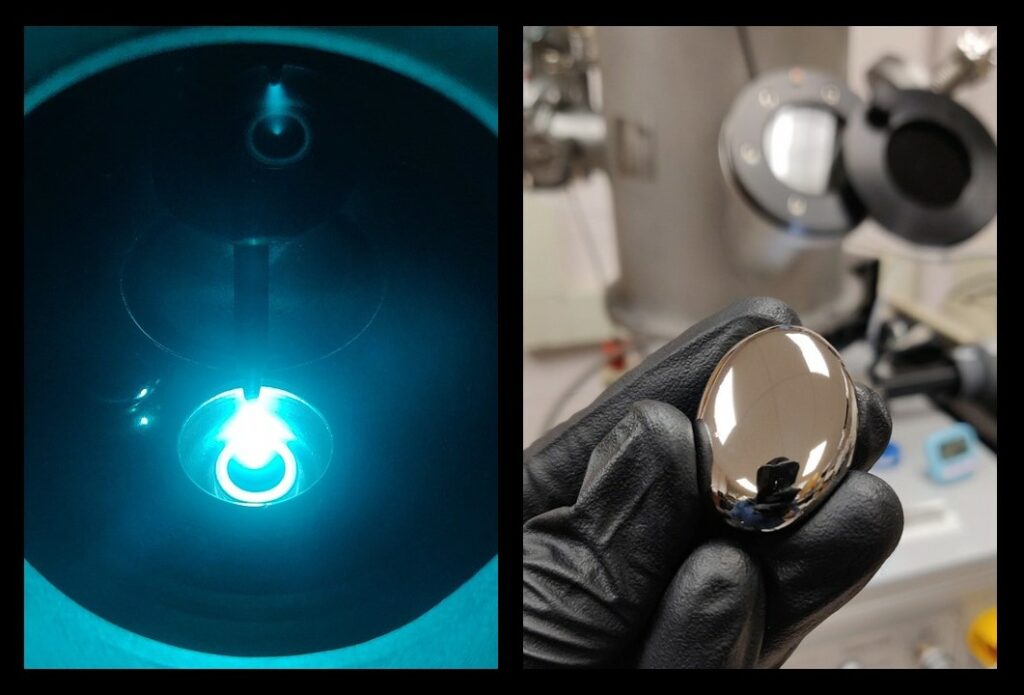
(Right) Metallic glass sample as it comes out of the arc-melter; the arc melter can be seen in the background.
Why should we care about metallic glass?
Metallic glasses are fundamentally cool, but in case that isn’t enough to peak your attention, they also have super powers that’d make Magneto drool. They have 2-3x the strength of steel, are incredibly elastic, have very high corrosion and wear resistance and have a mirror-like surface finish. So how can we apply these super metals to science? Well, NASA is already on it and is beginning to use metallic glasses as gear material for motors. While the Curiosity rover expends 30% of its energy and 3 hours heating and lubricating its steel gears to operate, Curiosity Jr. won’t have to worry about that with metallic glass gears. NASA isn’t the only one hopping onto the metallic glass train. Apple is trying to use these scratch proof materials in iPhones, the US Army is using high density hafnium-based metallic glasses for armor penetrating military applications, and some professional tennis and golf players have even used these materials in their rackets and golf clubs. But it took a long time to get these metallic glasses to the point where they’re now being used in rovers and tennis rackets.
Metallic glass: a history
Metallic glasses first appeared in the 1960’s when Jaskaran’s academic great grandfather (that is, his advisor’s advisor’s advisor), Pol Duwez, made them at Caltech. In order to achieve this special amorphous structure, a droplet of a gold-silicon alloy was cooled at a rate of over a million Kelvin per second with the end result being an approximately quarter sized foil of metallic glass, thinner than the thickness of a strand of hair. Fast forward to the ‘80’s, and researchers began producing larger metallic glasses. By the late ‘90’s and early 2000’s, the thickness of the biggest metallic glass produced had already exceeded 1000x the original foil thickness. However, with great size comes greater difficulty! If the metallic glass is too thick, it can’t cool fast enough to achieve an amorphous structure! Creating larger pieces of metallic glass has proven itself to be extremely challenging – and therefore is a great goal to pursue for graduate students and PI’s interested in taking on this challenge.
Currently, the largest pieces of metallic glasses are around 80 mm thick, however, they use and are based on precious metals such as palladium, silver, gold, platinum and beryllium. This makes them not very practical for multiple reasons. First, is the more obvious cost standpoint. Second, given the detrimental impact of mining rare-earth metals, efforts to minimize dependence on rare-earth metals can have a great positive impact on the environment.
World records you probably didn’t know existed until now
As part of Prof. Donghua Xu’s lab, Jaskaran is working on developing large-sized metallic glasses from cheaper metals, such as copper, nickel, aluminum, zirconium and hafnium. It’s worth noting that although Jaskaran’s metallic glasses typically consist of at least three metal elements, his research is mainly focused on producing metallic glasses that are based on copper and hafnium (these two metals are in majority). Not only has Jaskaran been wildly successful in creating glassy alloys from these elements, but he has also set TWO WORLD RECORDS. The previous world record for a copper-based metallic glass was 25 mm, which he usurped with the creation of a 28.5 mm metallic glass. As for hafnium, the previous world record was 10 mm which Jaskaran almost doubled with a casting diameter of 18 mm. And mind you, these alloys do not contain any rare-earth or precious metals so they are cost-effective, have incredible properties and are completely benign to the environment!
Excited for more metallic glass content? Us too. Be sure to listen live on Sunday February 6th at 7PM on 88.7FM, or download the podcast if you missed it. Want to stay up to date with the world of metallic glass? Follow Jaskaran on Twitter, Instagram or Google Scholar. We also learned that he produces his own music, and listened to Sephora. You can find him on SoundCloud under his artist name, JSKRN.
This post was written by Bryan Lynn and edited by Adrian Gallo and Jaskaran Saini.