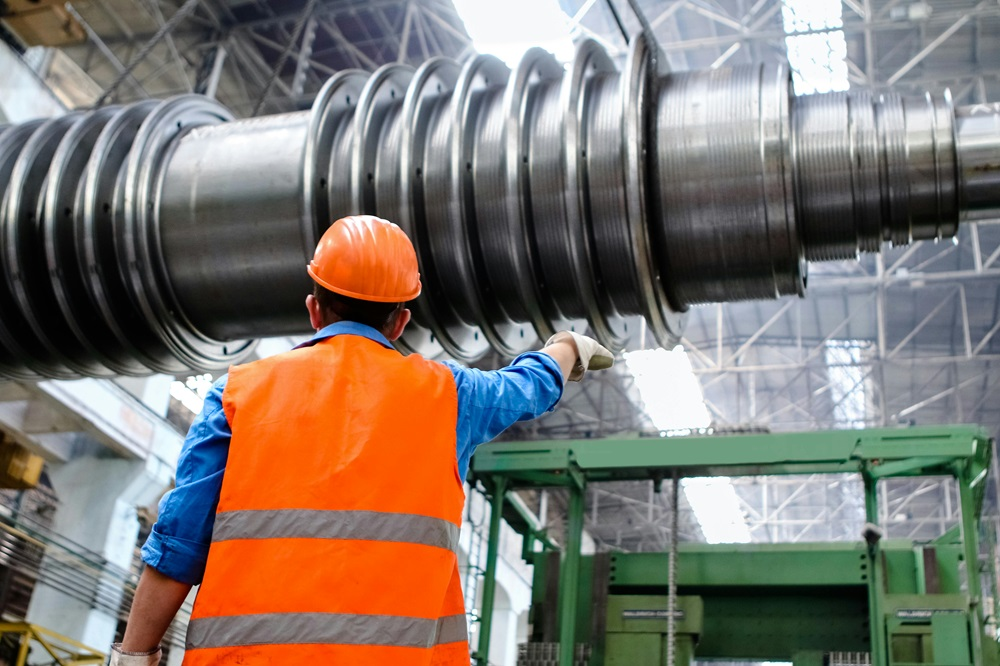
You hear it everywhere you turn: Industry 4.0, smart factories, the Industrial Internet of Things (IIoT). It can feel like the manufacturing industry is on the verge of a technological revolution. But is it really that simple? Are smart technologies just a passing trend, or are they truly the future of manufacturing? Let’s break it down.
Understanding the Shift: Why Smart Tech Matters
To understand the future, we must look at the challenges facing manufacturers today. These challenges go beyond simply producing goods.
- Efficiency: Manufacturers are constantly pressured to produce more with less – less waste, lower costs, and faster turnaround times.
- Quality Control: Maintaining consistent, high-quality output is crucial in today’s competitive market.
- Flexibility: Consumer demand is increasingly erratic. Manufacturers need to adapt quickly to new product lines and variations.
Smart technologies offer solutions to these challenges in ways traditional methods simply can’t match.
How Smart Technologies are Reshaping Manufacturing
Let’s look at some specific examples of how smart technologies are transforming the manufacturing landscape:
1. Data Analytics and Predictive Maintenance
Imagine knowing your machinery was about to have problems before it failed. Smart sensors in equipment can monitor performance indicators like temperature, vibration, and energy consumption. This data allows for predictive maintenance, minimizing downtime and costly repairs. Instead of reacting to breakdowns, manufacturers can proactively address potential issues, leading to significant cost savings and increased uptime.
2. Automation and Robotics
Robotics in manufacturing isn’t new. However, smart robots are taking automation to a new level. These robots can learn and adapt to changing environments, performing complex tasks with greater precision and efficiency. This isn’t about replacing human workers; it’s about freeing them from repetitive tasks and allowing them to focus on higher-value activities.
3. Digital Twins and Simulation
A digital twin is a virtual replica of a physical asset, process, or even an entire factory. This allows manufacturers to test new methods, experiment with different layouts, and optimize production – all in a risk-free virtual environment. Imagine being able to identify bottlenecks or test new equipment without affecting your actual production line. That’s the power of digital twins.
4. Improved Supply Chain Visibility
Smart technologies offer real-time tracking of materials and products throughout the supply chain. This leads to better inventory management, reduced waste, and improved responsiveness to disruptions. Imagine a world where you always knew the exact location of your raw materials and finished goods, allowing you to optimize delivery routes and minimize delays.
5. Customized Production
Consumers increasingly want personalized products. Smart technologies enable manufacturers to shift from mass production to mass customization. Think personalized clothing, custom-designed furniture, or even 3D-printed medical implants. This shift allows manufacturers to cater to individual customer needs and stay ahead of evolving market trends.
Overcoming the Barriers to Adoption
While the benefits of smart manufacturing are clear, some hurdles prevent widespread adoption. One major obstacle is the initial investment cost, which can be significant, especially for smaller companies.
There’s also a lack of skilled labor equipped to manage and maintain these advanced systems. Addressing these challenges will require a multi-faceted approach, including government incentives, industry partnerships, and educational programs to develop a future-ready workforce.
Securing the Smart Factory
Of course, as manufacturing gets “smarter,” we also have to get smarter about security. All those connected machines and data flowing back and forth create opportunities for cybercriminals. Imagine someone hacking your systems and altering your production processes remotely. Not a pleasant thought!
That’s why cybersecurity has to be a top priority for smart factories. It’s not just about protecting proprietary info anymore. We’re talking about securing the entire operational technology environment. Manufacturers will need solid security architectures, access controls, data encryption, you name it. And let’s not forget the human element – employee training and strict protocols are crucial for avoiding disastrous breaches.
The good news is that cybersecurity experts and technology providers are already teaming up to get ahead of the risks. By building security into smart manufacturing from the ground up, we can keep realizing all the amazing benefits without opening ourselves up to threats. It’s all about staying proactive and treating cybersecurity as a core part of smart factory operations.
The Real Question: Can You Afford Not to Adapt?
While some might view smart manufacturing as a significant investment, the cost of inaction is far greater. Companies slow to adopt these technologies risk falling behind their competitors in efficiency, quality, and market responsiveness.
Think of it this way: investing in smart technologies is like upgrading your toolbox. You’re not just getting new tools; you’re gaining the ability to work smarter, faster, and more effectively.
Consider, for example, the precision and control offered by techniques like Induction Heat Treatment from TeamInc.com, a process made even more efficient with smart integrations.
Embracing the Future of Manufacturing
The future of manufacturing is undeniably intertwined with smart technologies. It’s not just about keeping up; it’s about leveraging these tools to unlock new levels of efficiency, quality, and flexibility. The companies that embrace this transformation – investing in technology, upskilling their workforce, and adapting their strategies – will be the ones leading the way in the years to come.